Employee Workplace Safety
Manage and track all aspects of EH&S workplace safety including employee working locations, history, training requirements, incidents, accidents, causes, and the necessary corrective actions.
Platforms:
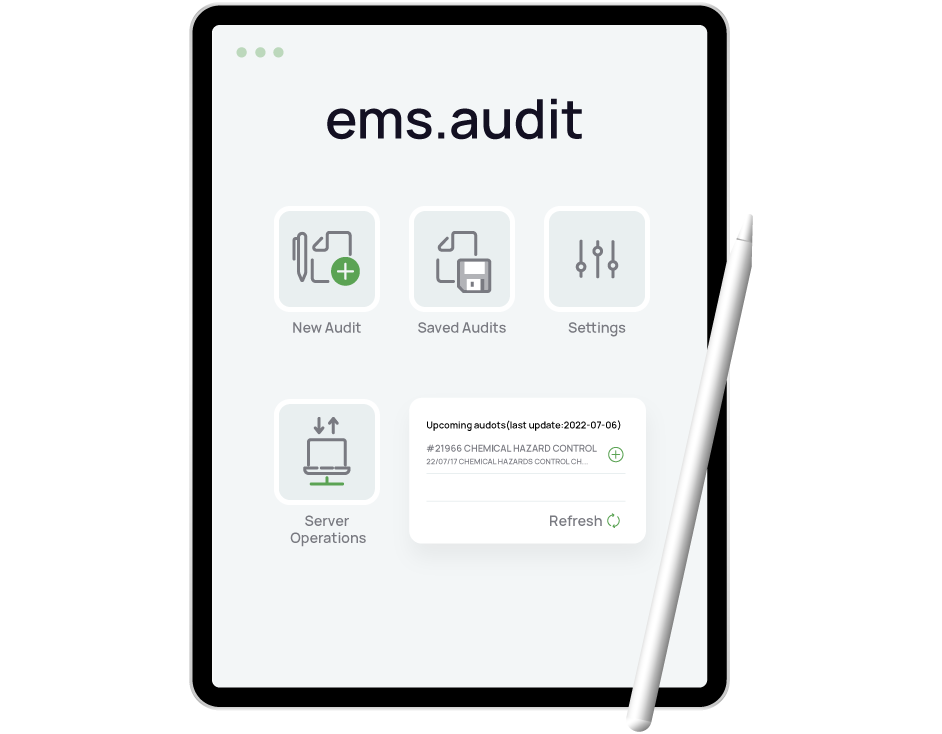
EH&S Software Customers
Many of the world’s leading organizations rely on Chemical Safety’s EMS software to help manage their EHS operations. Our customers are both large and small organizations, and they come from a wide variety of industries.
Workplace Safety Features
Manage and track all aspects of EH&S workplace safety including employee working locations, history, training requirements, incidents, accidents, causes, and the necessary corrective actions.
Employee Information
Define the employee’s workplace location and responsibilities.
Employee Training
Track training requirements and training frequency requirements with alerts and notifications.
Incidents & Accidents
Monitor, track and report workplace incidents and accidents with corrective actions.
Industrial Hygiene
Monitor, track and report worker and workplace industrial hygiene results.
OSHA Reporting
Create and report OSHA accident notifications and annual accident reports.
HR Reporting
AdHoc reporting system allows creating custom reports with virtually unlimited capabilities.
Audits & Inspections
Customizable inspection questionnaires, document and photograph difficiencies, automated corrective actions.
Audits & Inspections iPad App
Perform audits and inspections using our iOS mobile app for better mobility.
Product Description
Case Study
Manage and Improve Workplace Safety
Chemical Safety’s EMS employee workplace safety software supports the organizations needs as they relate to managing and tracking all aspects of environmental health and safety employee and workplace safety. It tracks employee working locations, history, and cross-references training requirements with target dates for re-training. This module records and reports workplace incidents, accidents, causes, and the necessary corrective actions.
Accidents are sometimes indicators of areas where safety improvements can be made. EMS software will help you identify the root cause of reported accidents, discover potential workplace hazards, identify past trends, and establish focused interventions that will prevent similar accidents from recurring.
Oversights in matters pertaining to workplace safety can be costly to your company in many ways. The investments of time and money that you make now will pale in comparison to the cost of an accident down the road. Fortunately, this software makes it easy for companies to be proactive about workplace safety and truly do the most they can to protect their personnel.
Employee Tracking
The EMS Tracking module manages detailed information about an employee including history, responsibilities, accident data, training requirements and status.
Employee Training
EMS has an intuitive tool that manages employee training requirements by job function, equipment used and training frequency requirements. By connecting specific job responsibilities to training requirements, employers and supervisors can have instant access to employees upcoming training or retraining needs through reports and automated email notifications.
Incidents and Accidents
The EMS- Accident / Incident module is a cost-effective and easy to use tool that can help you effectively protect the safety, health, and welfare of people engaged in your work or employment. This module will also facilitate compliance with OSHA standards. You can review previous or report new actionable incidents and keep a record in order to avoid unplanned events that adversely affect completion of your company’s operations. Use the EMS audit module in order to identify possible causes of the incidents recorded. Organize, initiate and apply corrective actions through the EMS task scheduler and calendar module that allow you to stay on top of safety-related events.
OSHA Regulatory Reporting
The EMS Employee Tracking module allows companies to easily and accurately track incidents and accidents that are OSHA reportable. You can quickly and easily report accidents to the Occupational Safety and Health Administration (OSHA), as required, as well as tabulate and report the annual OSHA 300 report easily and accurately.
Integrated Adhoc Reporting System
The EMS ad hoc reporting system provides on-demand custom reporting. It provides self-service integrated reports that customers can customize without extensive database knowledge. From simple to complex reporting the interface is easy to learn and use. While the reporting has great out of the box functionality, it is also easily edited depending on the users needs.
Safety Data Sheets Case Study
The Challenge
A leading manufacturing company in a heavy industry required twice-daily inspections of its production floors for proper waste pickup and also air emissions monitoring results, to ensure that the facility operated within permit limits.
The process to-date had been done manually, with paper forms and scheduling delays, as well as monitoring and corrective actions that did not meet corporate standards.
The Solution
Chemical Safety Software was tasked with implementing a software solution that automated the audit, inspection, monitoring and corrective action process for this large manufacturing operation.
The solution provided by Chemical Safety was the implementation of processes centered around our comprehensive chemical management software, Environmental Management Systems (EMS).
Chemical Safety configured EMS on a cloud-server, created customized audit and inspection questionnaires that were published on iPads, and customized the input forms to include scanning drums, shop floor locations and stacks to identify the different equipment and processes being inspected. Automated task processes were created to remind operators to perform the audits in a timely manner, and supervisors were notified when delays occurred. The responses to the audits were automatically uploaded and recorded in EMS, and whenever an adverse response was entered, an alert was sent to appropriate personnel for corrective action.
Achieve Environmental Compliance Objectives in Less Time
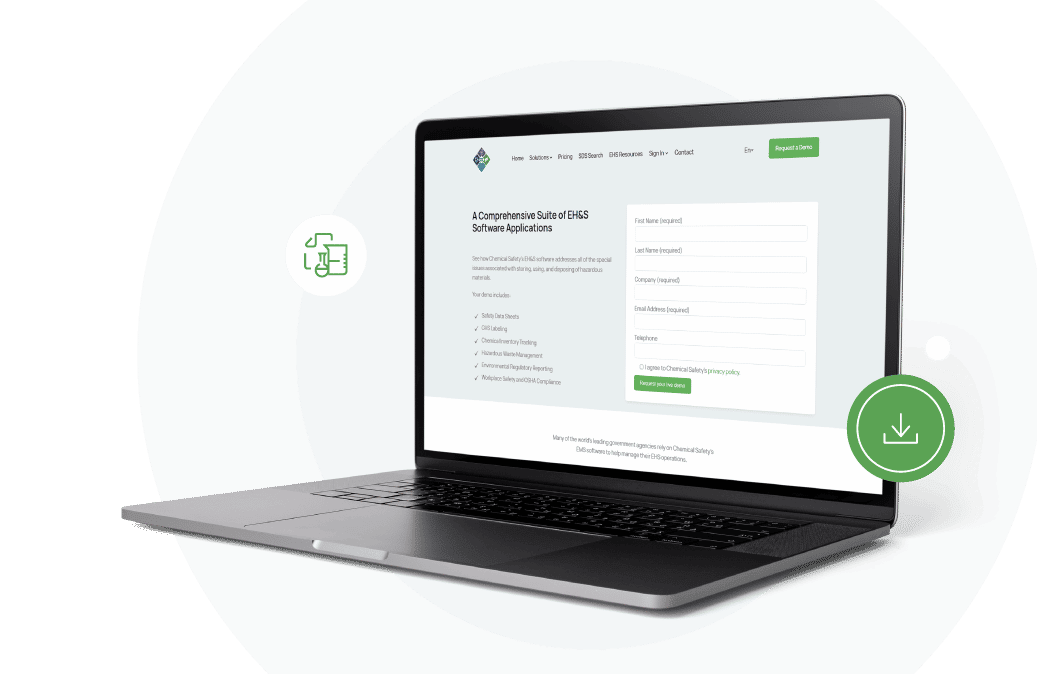